Figure lovers think of a new figure idea, make it a reality, and other figure lovers buy it. The world of figures gets more fascinating the deeper you go. To the shop owner of Gaccha, who’s been running the figure specialty shop in Nakano Broadway for 15 years, figures are “emotional support.” It’s a long and fervent process, from brainstorming to production, to make figures that mean so much to people.
This is the third and final part of our report on figure manufacturer Kotobukiya. This time, we consider the future of the figure industry.
These days, Japanese anime and manga are being broadcast and spread all across the globe. Because of this, the demand for figures is likely to increase. If this is the case, what will be the effect on how figures are produced? Will there be more sculptors and mold makers, or…? At Kotobukiya, they have a group concerned with thinking about questions like this: the Data Prototype Team.
The Ever-Evolving World of Figures
The Data Prototype Team was formed about about four years ago. They do their work in Santama Digital Labs, about a 5-minute walk from Kotobukiya’s headquarters. Just like the handmade prototype group, it is split into plastic model and figure sections. Data Prototype Team representative Mr. Ashizawa was kind enough to explain what this young team is all about.
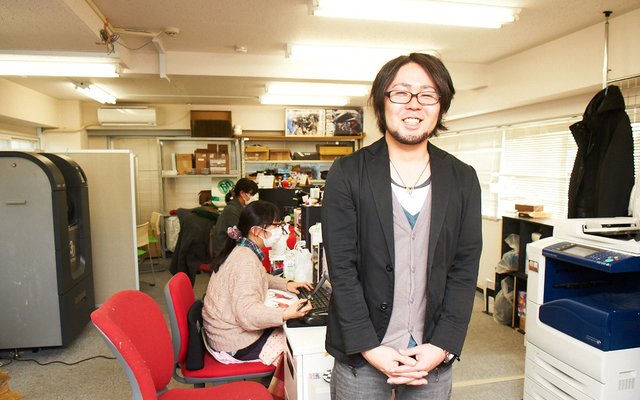
“We make prototypes on our computers and then output them with 3D printing. Even so, the core of what we do is essentially the same as the hand-made production team. While they use electric rotary tools and utility knives, we use a mouse and keyboard. That’s the only difference.” There were many unfamiliar tools placed around the Data Prototype Team workshop. One of which is called Freeform, a modelling tool that allows you to manipulate 3D models on screen as if you are making them by hand. The pen-shaped “mouse” has a spring to provide tension and virtually recreate the sensation of hand-made modelling. In this way, the 3D figure model on the PC can be created through a series of bumps and indentations. This technology is mostly used in figure making and other similar forms of 3D data production.

The second section of the Data Prototype Team is concerned with plastic models. This section does not use Freeform or ZBrush, but rather CAD (Computer Aided Design) technology in their work. This work does not involve a special 3D mouse or pen tablet, and can be done with a standard keyboard and mouse. Unlike the Freeform technology which is more about intuitive 3D modelling, this job involves drawing lines and manually inputting dimensions to create a 3D model. This technique is best suited for making robots, weaponry, and other mechanical figures and objects.
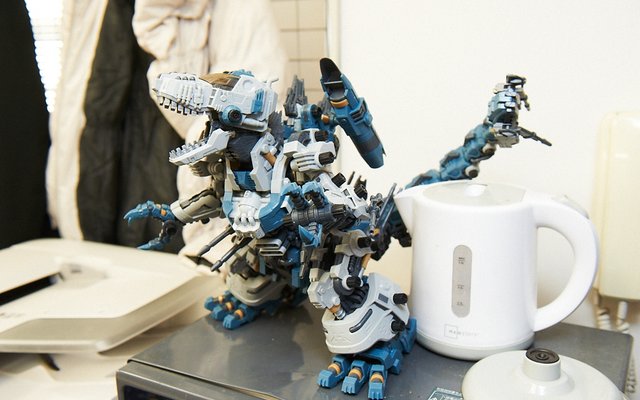
The completed prototypes produced by both teams are output through a 3D printer. Although the tools and methods like CAD and Freeform vary between the two sections, both of their prototypes are output in STL, a 3D printing data format. Once the STL data is sent to the printer, it’s just a matter of time before it becomes a tangible 3D model. However, time can be an issue. It takes about 1 hour to output 2.5 millimeters. Depending on the size of the figure, this process can take 40 hours or more. As of now, they only have one 3D printer, so even though they are able to produce digital prototypes relatively quickly, they sometimes end up waiting for the printer to output each one.
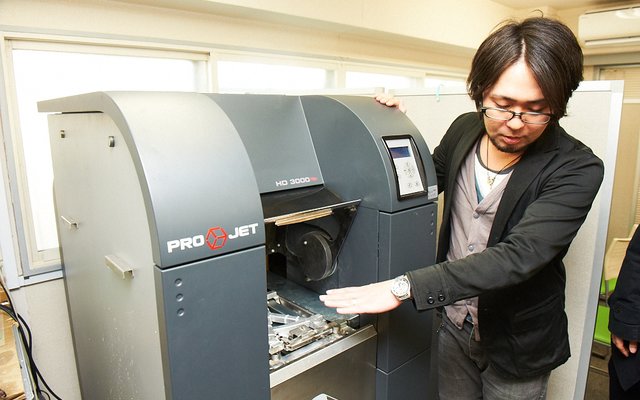
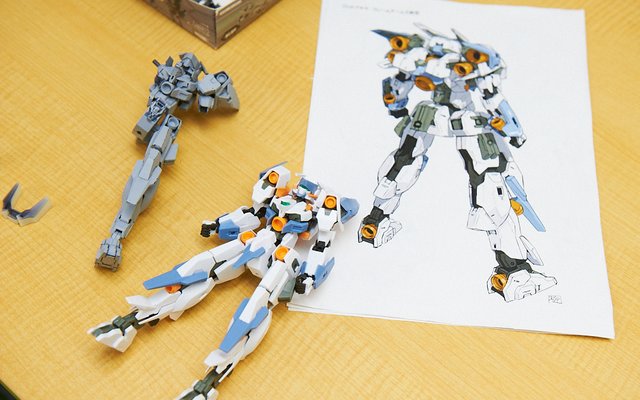
This HD3000plus 3D printer can print wax “support” sections at the same time (see the white area of this ear part). These supports are included to prevent the prototype from falling under its own weight and breaking during printing. These parts literally support the weight of the prototype and prevent material from falling into the undercuts as each layer is added.
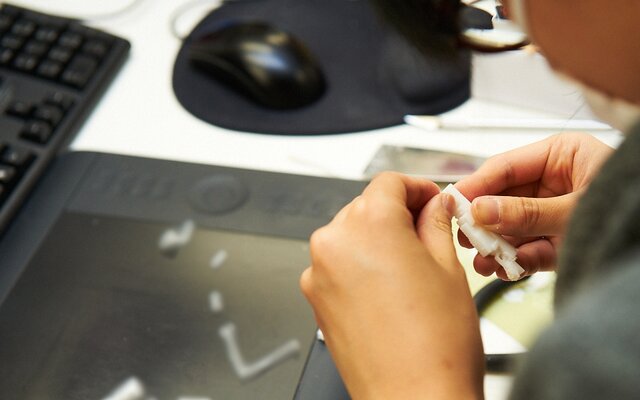
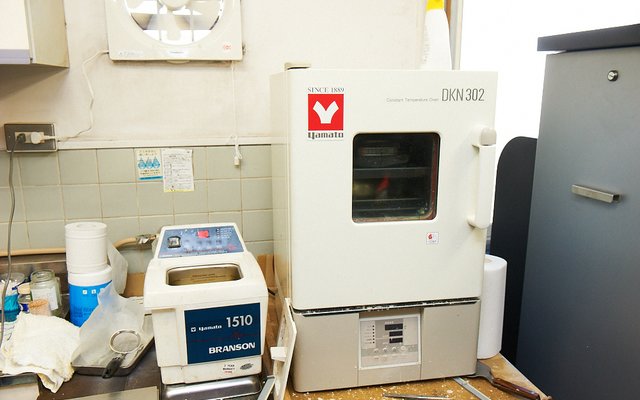
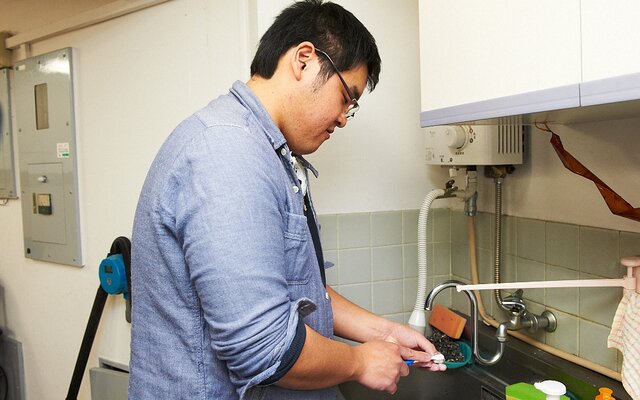
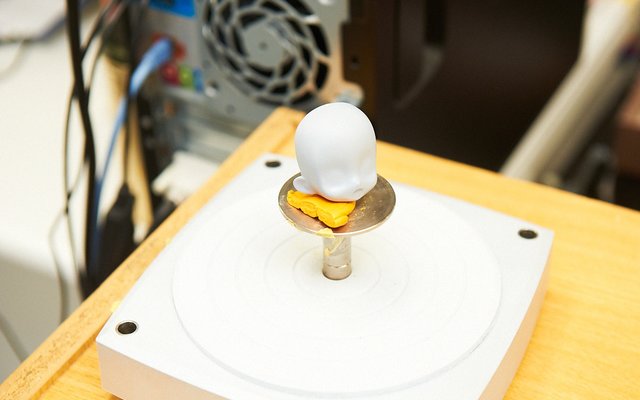
The finished output from the 3D printers stays true to the data and recreates a tangible copy down to the very last detail. The level of precision is so high that the margin of error is only 0.05 millimeters. Data prototypes are therefore very good at making perfectly symmetrical and round objects, as well as those that have gradual changes in size. The realm of possibilities in the figure world is likely to expand as the machines that produce them continue to reach an even higher level of accuracy.
The Value of Analog in a Digital World
"However,” Mr. Ashizawa continues, “data-based production methods are not perfect. There are still many things that are better and faster when done by hand. Body language and fabrics are a couple of prime examples. Data production methods are best suited for creating symmetrical shapes. This means that with many prototypes, once you’ve created half of it, you can make the rest of it from that half. Perfectly round shapes, evenly spaced patterns – those are the types of jobs that data production does best.”
He talked to us a bit more about analog and digital technology. “I think the proportion of handmade figures and plastic models to data prototypes is definitely going to lean heavily toward data production. This is because most young people these days have grown up using PCs since they were children. But even so, I don’t think handmade modelling will just disappear. In order to make a data prototype perfect, it still needs to be refined and painted by hand. I expect that it will become common to see production methods that are a synergy of manual and data-based output. We already are making some things by hand, digitizing them once, making the data symmetrical, and then outputting them again. It’s also common to use data production for only detailed parts and then do the rest by hand. We sometimes even do the opposite: use data methods to create a basic structure and then add detail to it by hand. It’s not a strict dualism of 'handmade vs. digital.’ Rather, a mix of both methods has proven to be the most efficient, I think."
We also talked to Ms. Tsuchiya from the Data Prototype Team. She says that after seeing digitally produced figure prototypes in Kotobukiya’s store in Akihabara, she felt that even with her clumsy fingers she could have potential with this method of figure making, so she joined the company. “It’s a young team, but I’m thankful that we are free to do things that we want. When making character figures, the nuance can change dramatically with even the slightest change, so it’s often difficult to find the right balance. Even when something looks good on screen, it often doesn’t turn out the same once it’s been output by the 3D printer, so it’s a struggle to decrease the gap between the screen image and final product.”
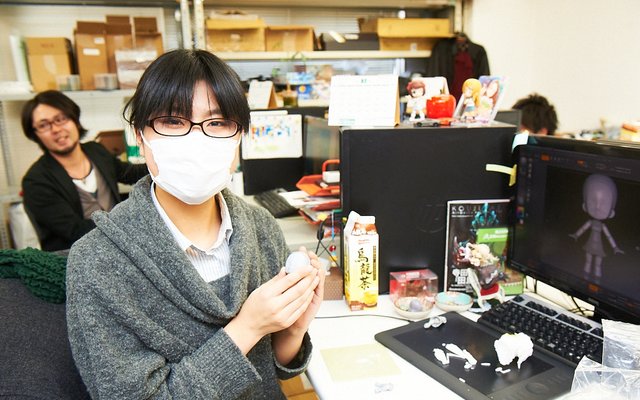
Bringing Figure Making into a New Era
"There’s a great deal of potential in 3D printing and 3D scanning technology. Aside from figures and industrial products, it’s also been gaining a lot of attention in the medical field. For example, take the CT scanner that you would find in a hospital. It uses X-rays or other forms of radiation to measure the shape of an object. So in principle, it’s just like a 3D scanner. If you were to take the data gathered about a particular organ in your body and send it to a 3D printer, you could potentially make a tangible copy that would allow you to better understand what part of the organ is afflicted before performing surgery on it. Now there are 3D printers that can output different types of resin simultaneously, so it would be possible to make the organ output in a transparent silicon material, use a different red resin to produce the capillaries and so forth until you’ve accurately reproduced the entire internal structure of the organ. This technology is also being used for heart valves. Since the shape of everyone’s heart valves are different, apparently it used to take at least a month to produce an artificial one with the methods we’ve used up until now. But with such 3D data technology as 3D printing, it can be made in just one or two days, I’ve heard,” Mr. Ashizawa explains.
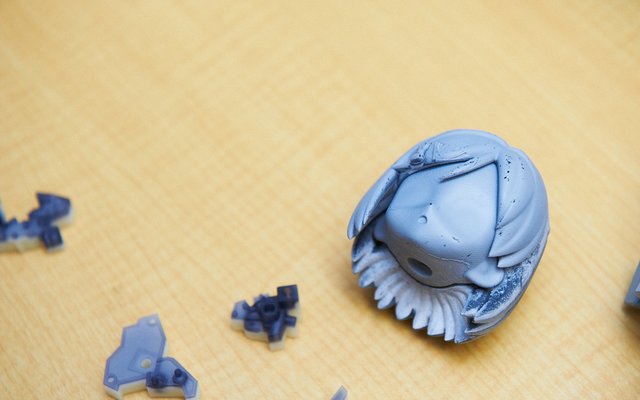
“There’s also the potential for this technology to be useful on the cellular level. By printing cells out layer by layer like a 3D printer and then letting it culture, you can produce different type of cells depending on the shape. Apparently that's the type of research that is being done right now in this area."
One doesn’t have to know much about 3D printing to understand its potential. Its range of potential applications are endless. “That’s right. In the comic Space Brothers 1 they talk about the idea of taking a 3D printer to the moon and using it to produce machinery and materials. Right now, resin is the most common material used in 3D printing, but ones that use titanium and other metals have come out as well. If those types of printers become more common, I think that the future of 3D printing can only get brighter."
Perhaps the day will come when we’ll see exquisite solid gold figures, or be able to buy figure data and print them out ourselves at home with our own 3D printers. That would definitely change the figure world as we know it. How will figures continue to evolve? Pay attention to Kotobukiya, as they will surely play a big part in shaping the future of the Japanese figure industry, whatever it may be.
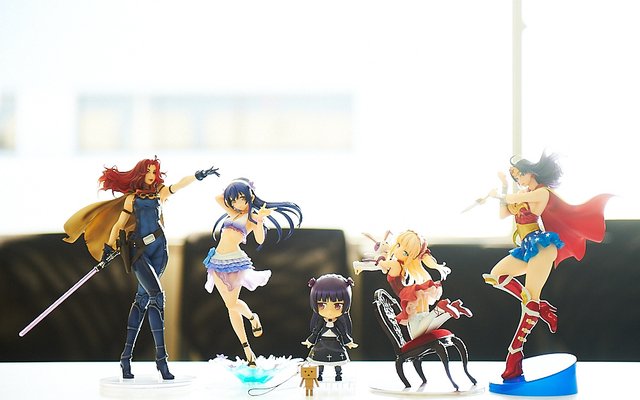
^1^ Chūya Koyama’s popular comic series about astronauts. It has been made into a live-action film and an anime.
This is a Tokyo Otaku Mode original article.